Top Notch Tips About Why Do VFD Convert AC To DC
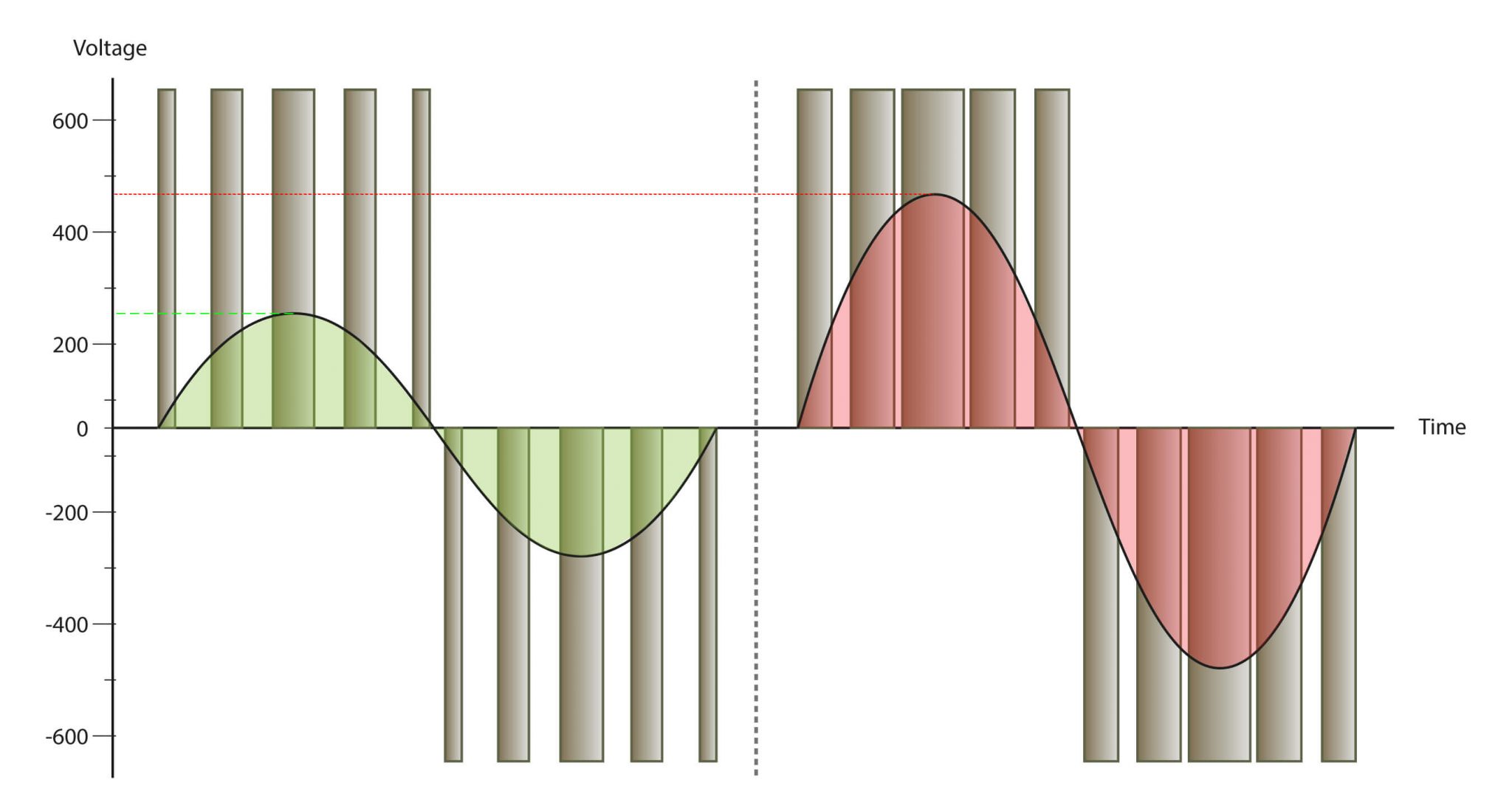
Unlocking the Mystery
1. The AC to DC Conversion
Ever wondered what goes on inside those unassuming boxes that control the speed of industrial motors? I'm talking about Variable Frequency Drives (VFDs), of course! At their heart, VFDs are all about controlling the frequency of the power supplied to a motor, which in turn controls its speed. But here's the thing: they can't directly manipulate AC (Alternating Current). That's where the magic — and the conversion — happens! To understand why VFDs convert AC to DC, we need to dive a little deeper into their inner workings.
Think of AC power like a wild river, constantly changing direction and intensity. DC (Direct Current), on the other hand, is like a calm stream, flowing steadily in one direction. VFDs need that steady stream to precisely control the motor. Trying to manipulate the "wild river" directly would be like trying to herd cats — chaotic and ultimately ineffective. So, the initial conversion to DC is a crucial first step in the process.
Essentially, the AC to DC conversion acts like a buffer. It allows the VFD to "clean up" the incoming power, removing any unwanted noise or fluctuations. This ensures that the motor receives a smooth, consistent flow of energy, which is essential for precise speed control and reliable operation. Without this conversion, you'd be stuck with jerky, unpredictable motor performance — not ideal for most industrial applications!
And lets be honest, dealing with inconsistent power is a recipe for disaster. It can lead to overheating, reduced motor lifespan, and all sorts of other headaches. The AC to DC conversion helps mitigate these risks, ensuring that the motor operates within safe and optimal parameters. Its all about creating a stable foundation for further manipulation.
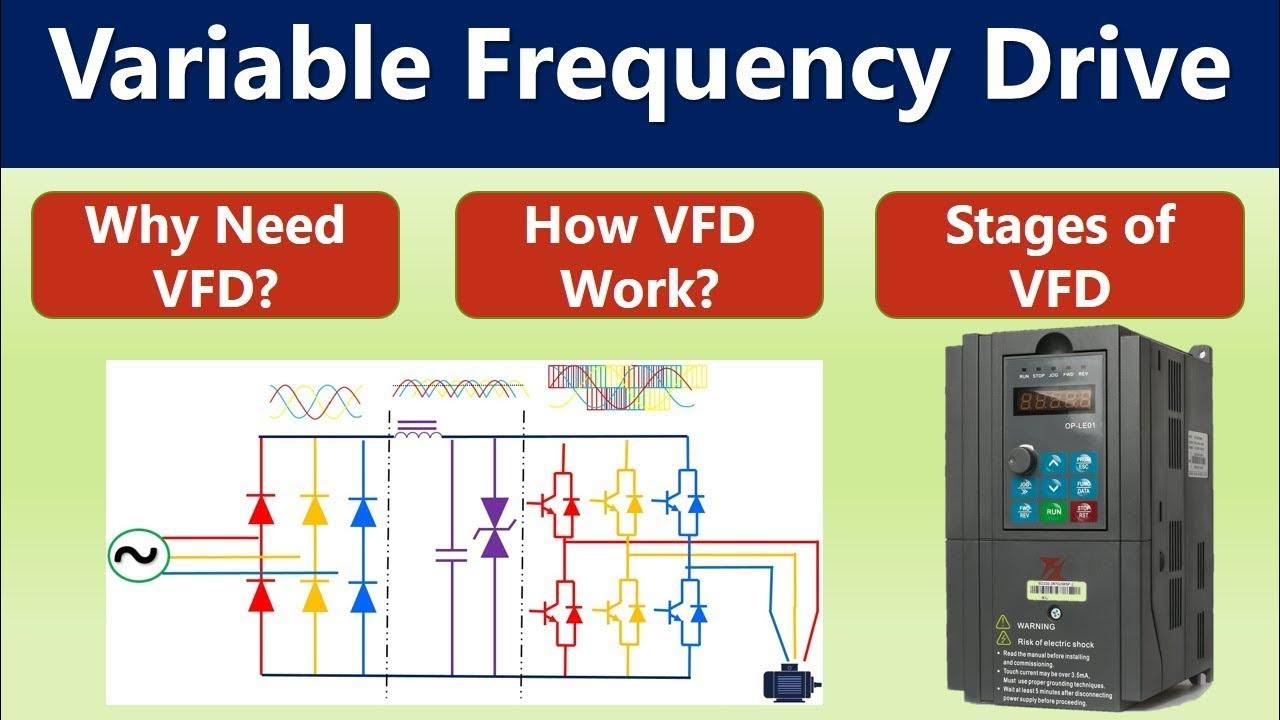
Breaking Down the VFD
2. Rectification
Okay, so we know AC gets converted to DC. But how does that actually happen? The first stage is called rectification. This is where diodes, acting like one-way electrical valves, step in to block the negative portion of the AC waveform. Imagine a gate that only allows water to flow in one direction — that's essentially what diodes do with electricity.
The result isn't a perfectly smooth DC signal just yet. Instead, you get a pulsating DC, sort of like a series of bumps. Its a step in the right direction, but still not quite the steady stream were aiming for. Think of it as the rough draft before the final polished version.
This "bumpy" DC isn't very useful on its own for precisely controlling a motor. It's still too variable and unpredictable. That's why we need the next stage — smoothing!
You might be wondering why we even bother with this intermediate step. Well, rectification is a relatively simple and efficient way to eliminate the negative portion of the AC waveform. It's the foundation upon which the rest of the process is built. Without it, we'd be trying to build our DC foundation on shifting sands!
3. Filtering
Alright, we've got our pulsating DC thanks to the rectifier. But as we mentioned before, it's still too bumpy. Think of it like a freshly paved road that still has some uneven patches. That's where filtering comes in! Capacitors, those handy little energy storage devices, are the key players in this stage.
Capacitors act like reservoirs, storing energy during the peaks of the pulsating DC and releasing it during the valleys. This smooths out the waveform, creating a much cleaner and more consistent DC signal. Imagine filling in those uneven patches on the road to create a smooth, even surface. That's what capacitors do for electricity!
The result is a stable DC voltage that the VFD can then use to create a variable frequency AC signal. This clean DC is absolutely critical for precise motor control. Without it, the motor would experience erratic speeds and potentially even damage.
Think of the filtering stage as the heart of the VFD's power supply. It's where the rough, pulsating DC is transformed into the smooth, steady stream of energy that powers the rest of the system. It's like taking a sip of cool water on a hot day — refreshing and essential for optimal performance!
4. Inversion
Now for the grand finale! We've converted AC to DC, smoothed it out, and now it's time to convert it back to AC. But this time, it's AC with a twist! The key here is a set of electronic switches, typically transistors or IGBTs (Insulated Gate Bipolar Transistors), that rapidly turn the DC voltage on and off. This creates a pulsed AC waveform.
By controlling the speed at which these switches turn on and off, the VFD can precisely control the frequency of the output AC signal. This allows the VFD to vary the motor's speed, providing the flexibility and control that is so vital in many industrial applications. Imagine you're controlling the flow of water through a series of valves — that's essentially what the switches are doing with the DC voltage.
These pulsed AC waveforms aren't perfectly smooth sine waves (the ideal shape for AC power), but they approximate it well enough for most applications. Advanced VFDs use sophisticated techniques like Pulse Width Modulation (PWM) to create even smoother waveforms, minimizing harmonics and improving motor performance. Its about fine-tuning the "pulsed" signal to closely resemble a true sine wave.
This inversion stage is the brain of the VFD, orchestrating the precise control of the motor. Its where the magic really happens, transforming a steady DC stream into a dynamic AC signal that can be tailored to meet the specific needs of the application. Without it, we'd be stuck with fixed-speed motors — a far less versatile and efficient solution.
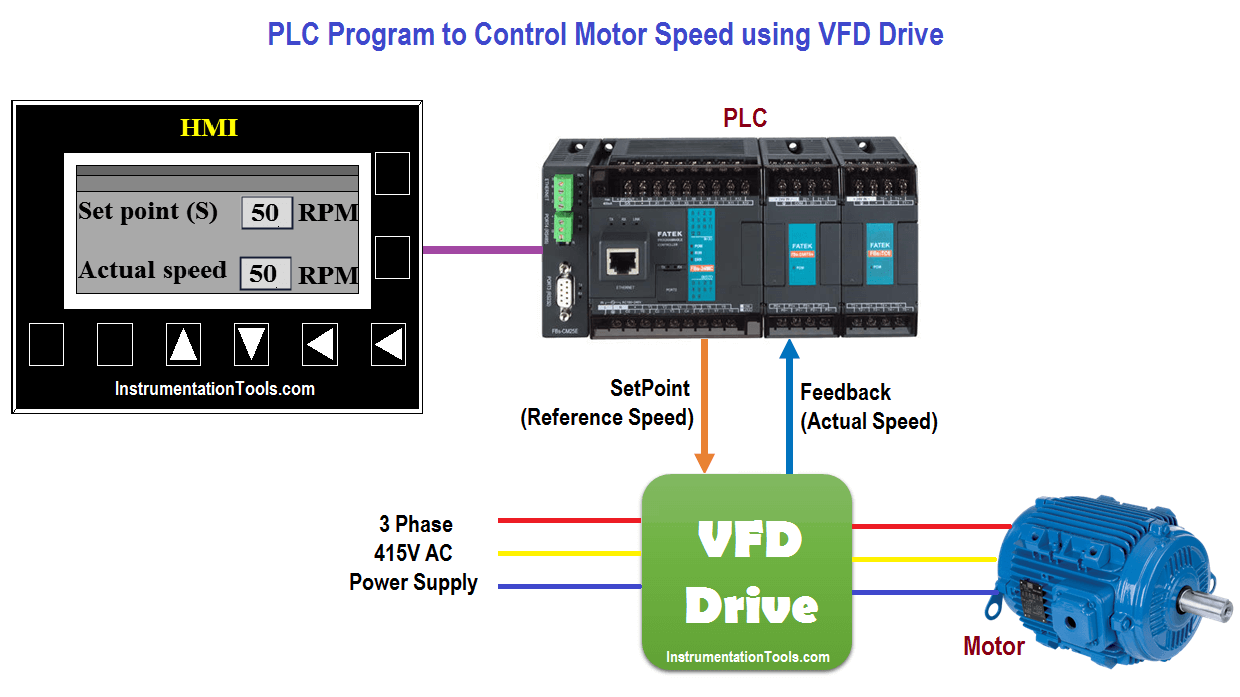
Wiring Vfd Motor Control Circuit Diagram / Variable Speed Drives An
Why Not Just Directly Manipulate AC?
5. The Challenge of Direct AC Control
You might be thinking, "Why go through all this trouble of converting AC to DC and back again? Why not just directly manipulate the AC signal?" That's a valid question! The simple answer is that it's extremely difficult, and typically less efficient and less precise.
Directly controlling the frequency and voltage of AC power requires complex and expensive circuitry. It's like trying to change the direction of a speeding train — it requires a lot of force and specialized equipment. The AC to DC conversion provides a much more manageable and efficient way to achieve the same result.
Another challenge with direct AC manipulation is dealing with reactive power. AC circuits have inductance and capacitance, which cause the current and voltage to be out of phase. This creates reactive power, which doesn't do any useful work but still circulates through the circuit, increasing losses and reducing efficiency. The AC to DC conversion helps to decouple the frequency control from the power supply, reducing the impact of reactive power.
Think of it like trying to steer a boat directly with the rudder versus using an engine. The rudder alone can be difficult to control, especially in rough waters. The engine provides the power and control needed to navigate effectively. The AC to DC conversion is like the engine in this analogy, providing the power and control needed to precisely manipulate the motor's speed.
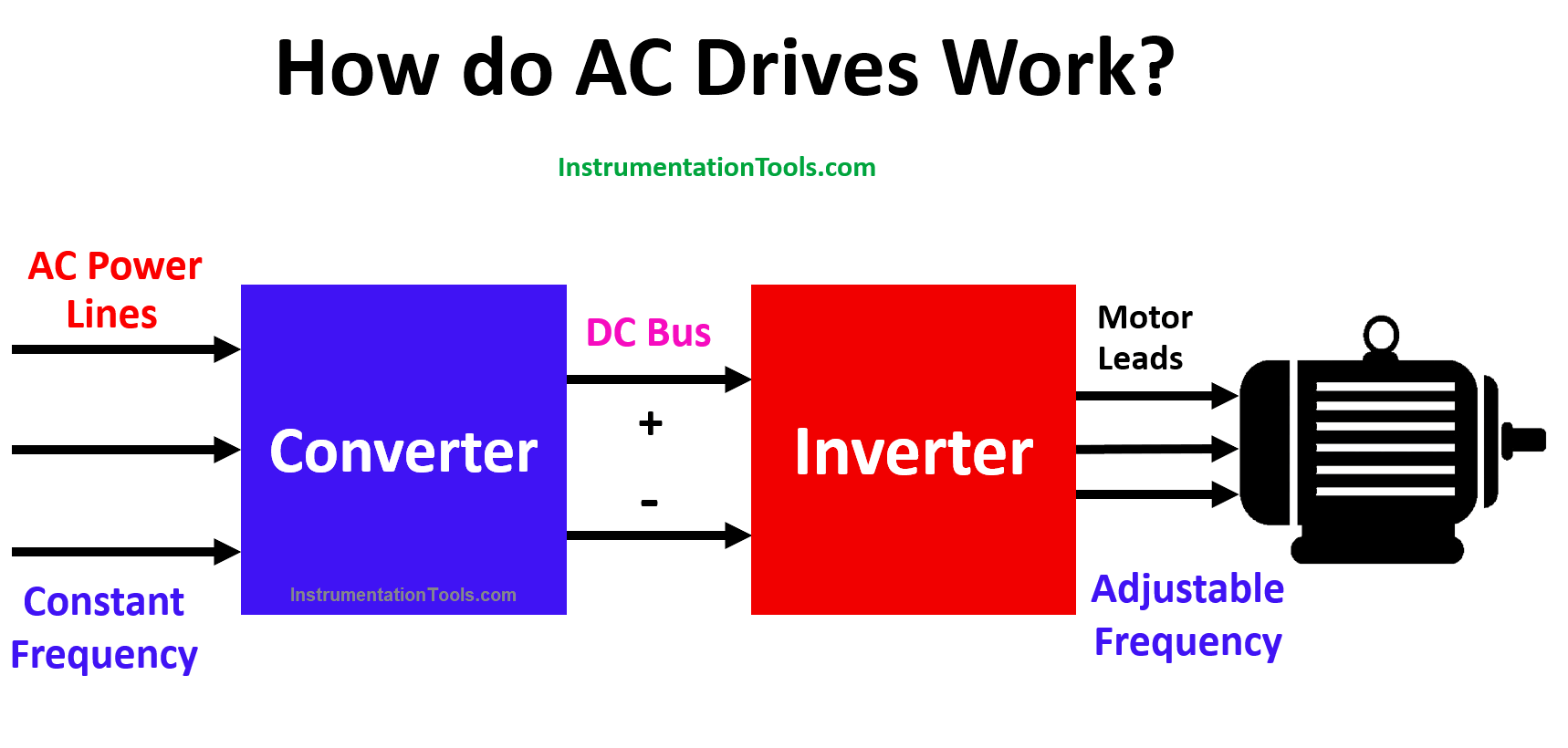
How Do AC Drives Work? Variable Frequency Drive (VFD)
The Benefits of the AC to DC Conversion in VFDs
6. Efficiency, Control, and Motor Protection
So, we've established that VFDs convert AC to DC for a good reason. But what are the actual benefits of this approach? Well, the advantages are numerous! Perhaps the most significant is improved efficiency. By controlling the motor's speed, VFDs can reduce energy consumption, especially in applications where the motor doesn't need to run at full speed all the time. This translates into significant cost savings and a reduced environmental impact.
Another key benefit is precise motor control. VFDs allow for smooth acceleration and deceleration, preventing sudden jolts that can damage equipment. They also provide precise speed regulation, ensuring that the motor operates at the optimal speed for the application. It's like having cruise control for your motor, maintaining a steady speed regardless of changes in load.
VFDs also offer motor protection. They can detect and respond to overcurrent, overvoltage, and other fault conditions, preventing damage to the motor and extending its lifespan. Its like having a built-in safeguard, protecting your motor from harm.
In short, the AC to DC conversion is the foundation upon which the many benefits of VFDs are built. It's a crucial step in providing efficient, precise, and reliable motor control. Its not just about converting power; its about unlocking a world of possibilities!
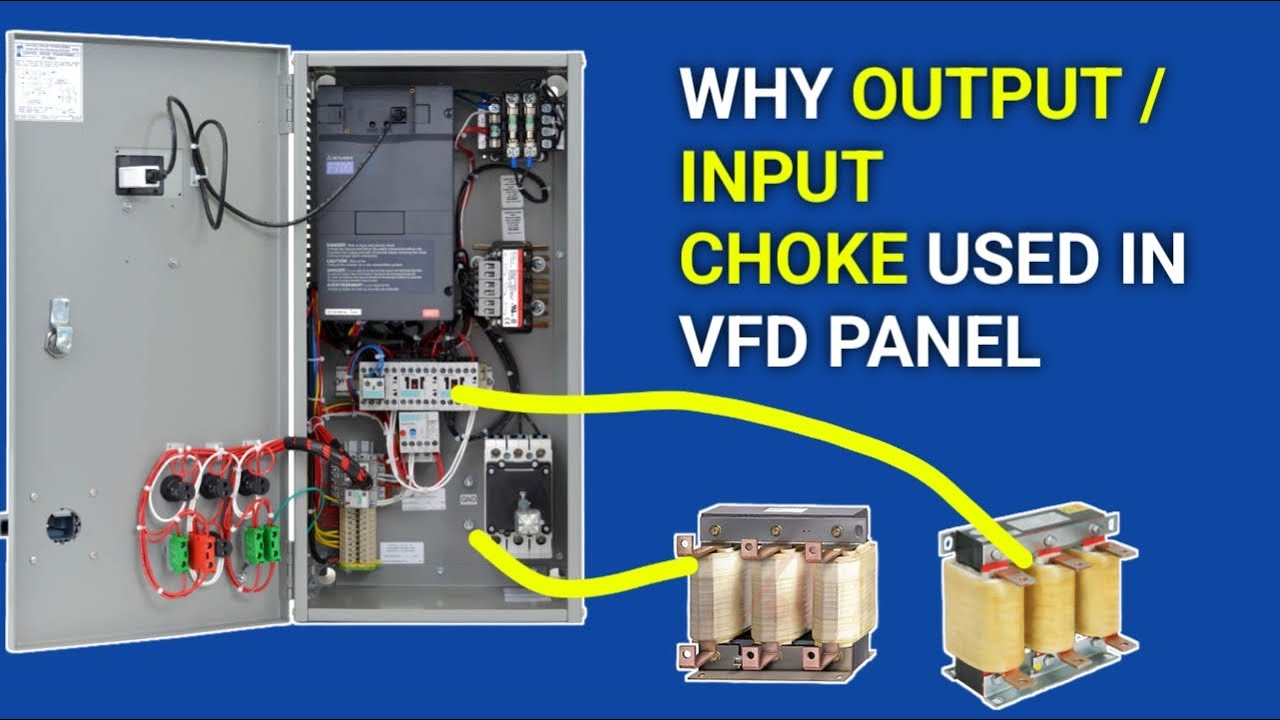
Electrical Panel Choke At Melody Davis Blog
FAQ About VFDs and AC to DC Conversion
7. Your Burning Questions Answered
Let's tackle some common questions about VFDs and their AC to DC conversion process.
Q: Why can't I just use a transformer to control a motor's speed?A: Transformers only change voltage, not frequency. Motor speed is directly related to frequency, so a transformer won't help you control speed. Plus, reducing voltage too much can damage the motor.
Q: Are all VFDs the same?A: No, there are different types of VFDs with varying levels of sophistication and features. Some use different switching technologies or advanced control algorithms to improve performance and efficiency.
Q: Can I use a VFD on any motor?A: While VFDs are compatible with many AC induction motors, it's crucial to ensure the motor is inverter-duty rated or suitable for VFD operation. Check the motor's specifications and consult with a qualified electrician to ensure compatibility.
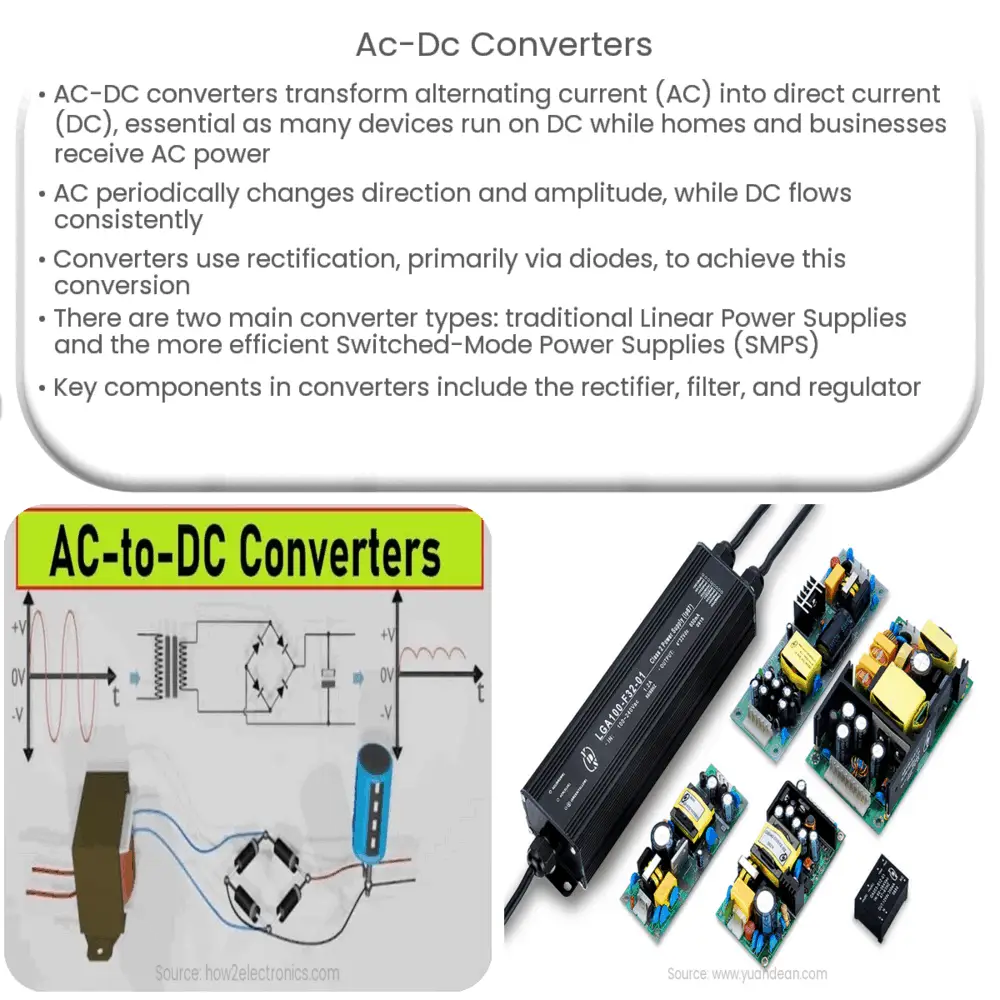